Understanding the Cost Dynamics of tin can in B2B Procurement
Introduction
In the realm of B2B procurement, particularly in the packaging industry. Understanding the factors that influence the cost of products is essential for effective decision-making. At Jinfeng, we specialize in producing tin boxes. However, clients often inquire about the reasons behind the varying costs of seemingly similar tin boxes. This comprehensive article aims to demystify the factors affecting tin box pricing. We focused on quality, cost-effectiveness, and efficiency. We have over 15 years experience on manufacturing tin can.
Quantity: The Scale of Tin Can Economy
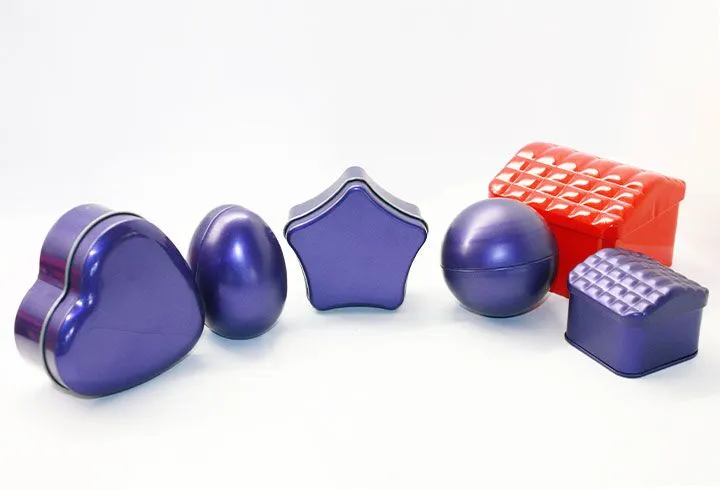
The Impact of tin can MOQ on Pricing
The concept of Minimum Order Quantity (MOQ) is a critical aspect in manufacturing, particularly in the tin box industry. MOQ refers to the lowest quantity of a product that a supplier is willing to sell. For tin boxes, the MOQ is directly tied to the printing process of the tinplate. This is because the setup cost for printing is relatively high. Therefore, ordering below the MOQ leads to a higher cost per unit.
Bulk Orders and Cost Efficiency
Bulk orders play a significant role in reducing the cost per unit. This is due to the economies of scale, where the average cost per unit decreases as the quantity increases. Larger orders allow for more efficient use of materials and labor, reducing waste and increasing productivity. For B2B buyers, understanding the significance of order quantity can aid in strategic planning.
Thickness: A Critical Tin Can Component
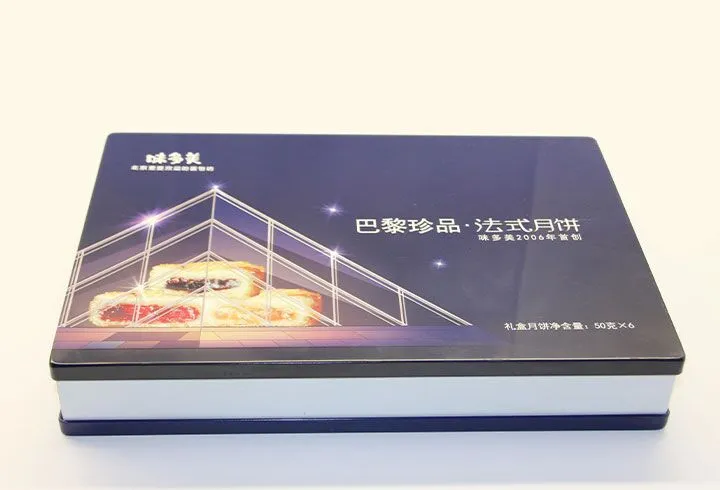
Thickness and Its Functional Implications
The thickness of the tinplate used in manufacturing tin boxes is a vital factor in determining the cost. Thicker tinplates offer increased durability and strength, making them suitable for heavier or more valuable contents. The choice of thickness is often dictated by the intended use of the tin box. For instance, a tin box designed for delicate items like electronics or luxury goods would require a thicker and more robust material compared to one intended for lightweight items.
Material Costs and Selection
The cost of the material is directly influenced by its thickness. Thicker materials are more expensive due to the increased amount of raw material used and the additional processing required. The choice of material thickness must strike a balance between the functional requirements of the tin box and the budget constraints of the buyer.
Manufacturing Tin Can Processes and Customization
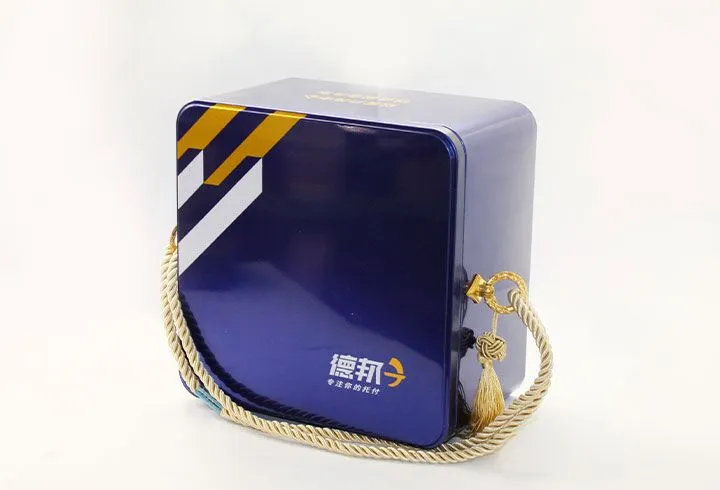
Standard vs. Custom Processes
The manufacturing process of tin boxes can vary significantly depending on the design and customization requirements. Standard designs using existing tooling are generally more cost-effective. However, custom designs, which may include unique shapes, embossing, debossing, or special printing techniques, entail additional processes and costs. Each additional process adds complexity and time to the manufacturing, impacting the overall cost.
The Role of Technology and Innovation
Advancements in manufacturing technology have allowed for more intricate designs and customization options. However, these innovations also come with increased costs. For example, digital printing offers high-quality, customizable prints but at a higher cost compared to traditional lithography. As a procurement officer, understanding the capabilities and costs associated with these technologies is essential for making informed decisions that align with both quality expectations and budgetary limitations.
Material Costs: A Global Perspective
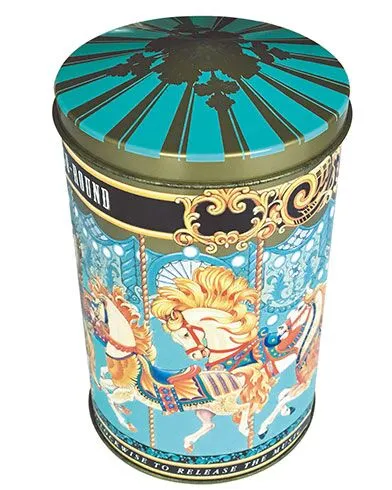
Fluctuations in Raw Material Prices
The cost of raw materials, primarily tinplate, is a significant component of the overall cost of tin boxes. These prices are subject to global market fluctuations, influenced by factors such as supply and demand dynamics, geopolitical events, and economic conditions. As a result, the cost of tin boxes can vary over time, reflecting these market changes.
Sourcing Strategies and Cost Implications
Effective sourcing strategies can mitigate the impact of material cost fluctuations. As a manufacturer, we continuously monitor market trends and work with a network of suppliers to ensure the best possible material prices. For B2B buyers, understanding these sourcing strategies and their implications on cost can provide a competitive edge in negotiations and procurement planning.
Labor Costs and Manufacturing Efficiency
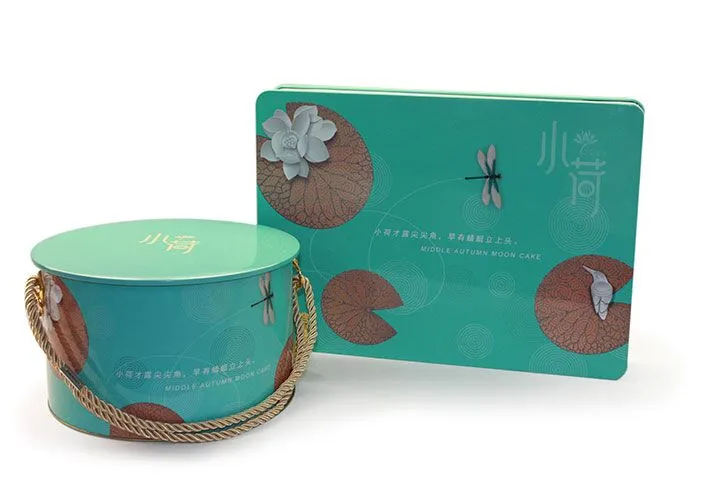
Labor costs contribute significantly to the overall cost of tin boxes. These costs are influenced by the complexity of the manufacturing process, the skill level required, and the labor market conditions in the manufacturing region. More complex designs and customizations require skilled labor, which increases the labor cost component of the product.
Efficiency and Automation
At Jinfeng, we leverage automation and efficient manufacturing processes to optimize labor costs. Automation in certain stages of production reduces the need for manual labor, thereby controlling costs while maintaining high-quality standards. Understanding these aspects of manufacturing efficiency can help B2B buyers appreciate the balance between cost, quality, and labor practices.
Packaging and Logistics: The Hidden Tin Can Manufacturing Costs
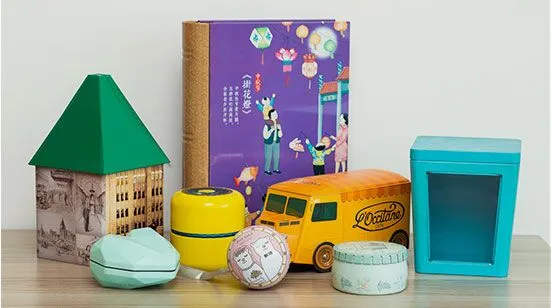
Packaging is an often-overlooked aspect that can impact the cost of tin boxes. The type of packaging used not only protects the product during transportation but also adds to the overall weight and volume, affecting shipping costs. We offer a range of packaging options, each with different cost implications, allowing buyers to choose the most suitable and cost-effective solution.
Logistics and Transportation
The cost of logistics and transportation is a critical component, especially in international trade. Factors such as distance, shipping method, and current freight rates play a significant role in determining the final delivered cost of the tin boxes. Efficient logistics management, including the selection of reliable shipping partners and optimization of shipping routes, is key to controlling these costs.
The Importance of Certifications and Compliance
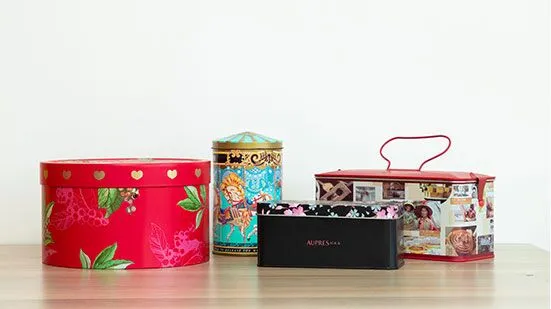
Compliance with International Standards
Certifications and compliance with international standards can influence the cost of tin boxes. Products that meet specific standards, such as food safety or environmental regulations, may require additional testing and certification processes, adding to the cost. However, these certifications are crucial for certain markets and can be a deciding factor for buyers concerned with quality and safety.
Balancing Compliance and Cost
At Jinfeng, we ensure that our products comply with relevant international standards, providing our clients with the assurance of quality and safety. While this can add to the cost, it is a necessary investment for accessing certain markets and maintaining a reputation for quality.
Market Trends and Customer Preferences
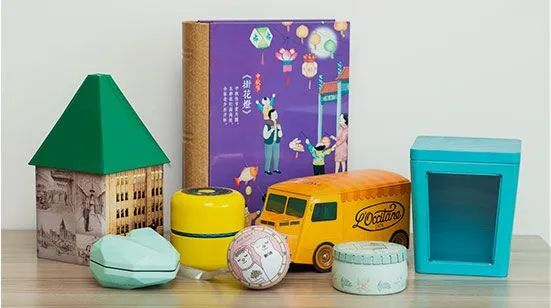
Adapting to Changing Market Dynamics
Market trends and customer preferences can also affect the cost of tin boxes. The demand for eco-friendly or innovative designs can lead to the adoption of new materials and processes, impacting the cost structure. Staying abreast of these trends and adapting to customer preferences is essential for remaining competitive in the B2B market.
Customization and Branding Opportunities
Customization and branding are important aspects for many B2B buyers, offering opportunities for differentiation in the market. The ability to customize tin boxes with company logos, specific colors, and unique designs is a value-added service that we provide. While this customization adds to the cost, it also offers significant branding and marketing benefits for the buyer.
Conclusion: A Comprehensive Cost Perspective
In conclusion, the cost of tin boxes is influenced by a myriad of factors, ranging from quantity and material thickness to manufacturing processes, labor costs, logistics, compliance, and market trends. As a B2B buyer, understanding these factors is crucial for making informed procurement decisions that balance quality, cost, and market needs.
At Jinfeng, we are committed to providing our clients with high-quality, cost-effective tin box solutions that meet their specific requirements. Our expertise in navigating these cost factors, coupled with our focus on customer service and quality, makes us a preferred partner in the tin box industry. Visit our Facebook for more information.